1. Problem description
In the scene of re-entry, an object with a shape close to the capsule has been analyzed using the DSMC method for different Mach numbers. The variation of parameters such as surface heat flux, surface pressure, and shear stress. The variation of temperature and density in the flow domain is discussed.
2. Methodology
Using Ar gas with VSS model.
d_ar | m_ar | gamma | k_b | n_dens | v_sound | MFP |
---|---|---|---|---|---|---|
4.11e-10 | 6.635909e-26 | 5/3 | 1.380649e-23 | 3.46E18 | 322.53 | 0.3851 |
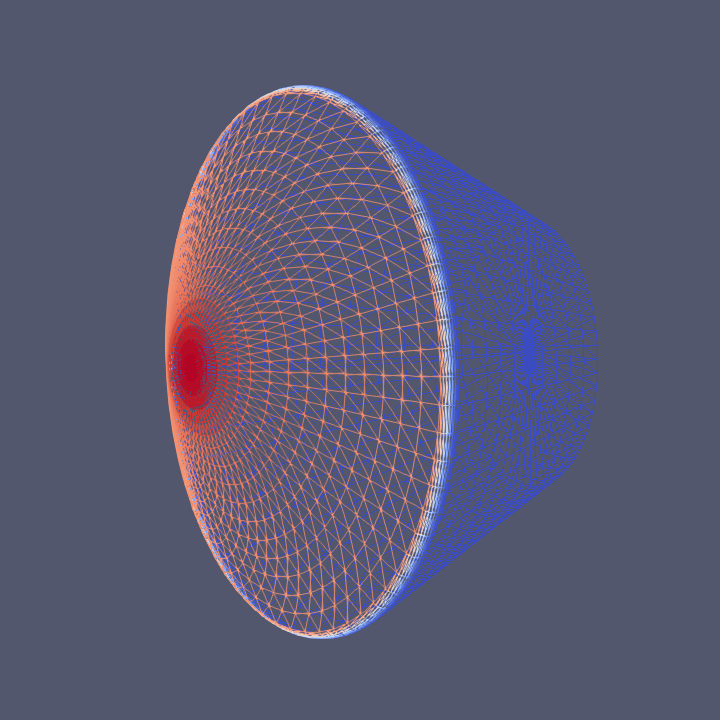

The outline of the capsule is $0.56\times0.78\times0.78$ in the simulation unit. Interpolate the capsule surface to get more detailed data. Refine and coarsen the grid in the transition state by using the adapt_grid
command every 100 steps. For reducing computation requirements, an axisymmetric 2D simulation was used. With initial conditions:
temp_gas | temp_wall | surf_collide | l_box | h_box | particle/grid | l_grid | t_step |
---|---|---|---|---|---|---|---|
300K | 300K | diffuse | 3.2 | 1.6 | 200 | 0.08 | 0.0001 |
The boundaries are set as emitting surfaces. The grid was set to $40\times20$ as in the image below.
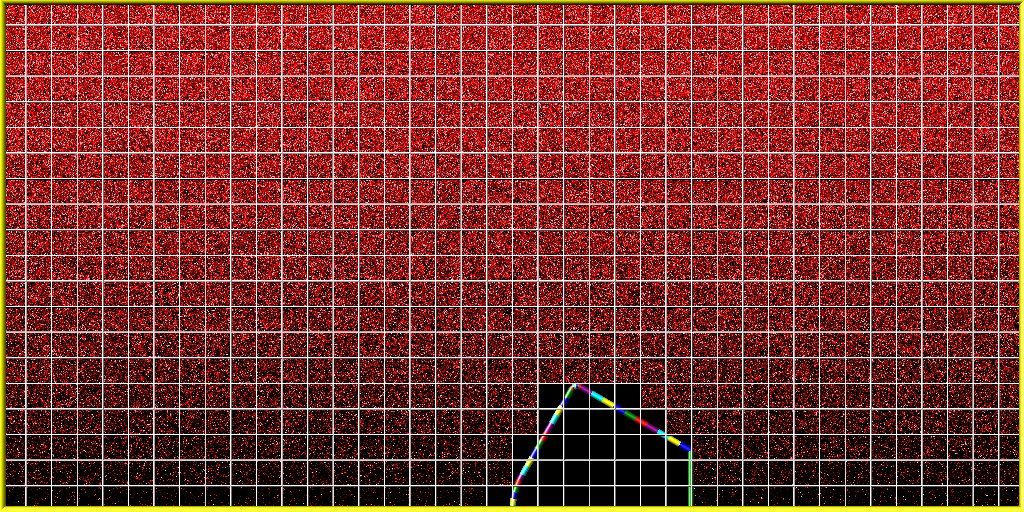
Compute 1E4 steps for transient and refinement. Then, run 1E4 steps more for steady results. Skips every 10 steps and takes 1000 samples to average.
3. Results and discussions
From left to right, they are the result of Mach2, Mach4, Mach8, and Mach12.
(i) Temperature and surface total energy flux
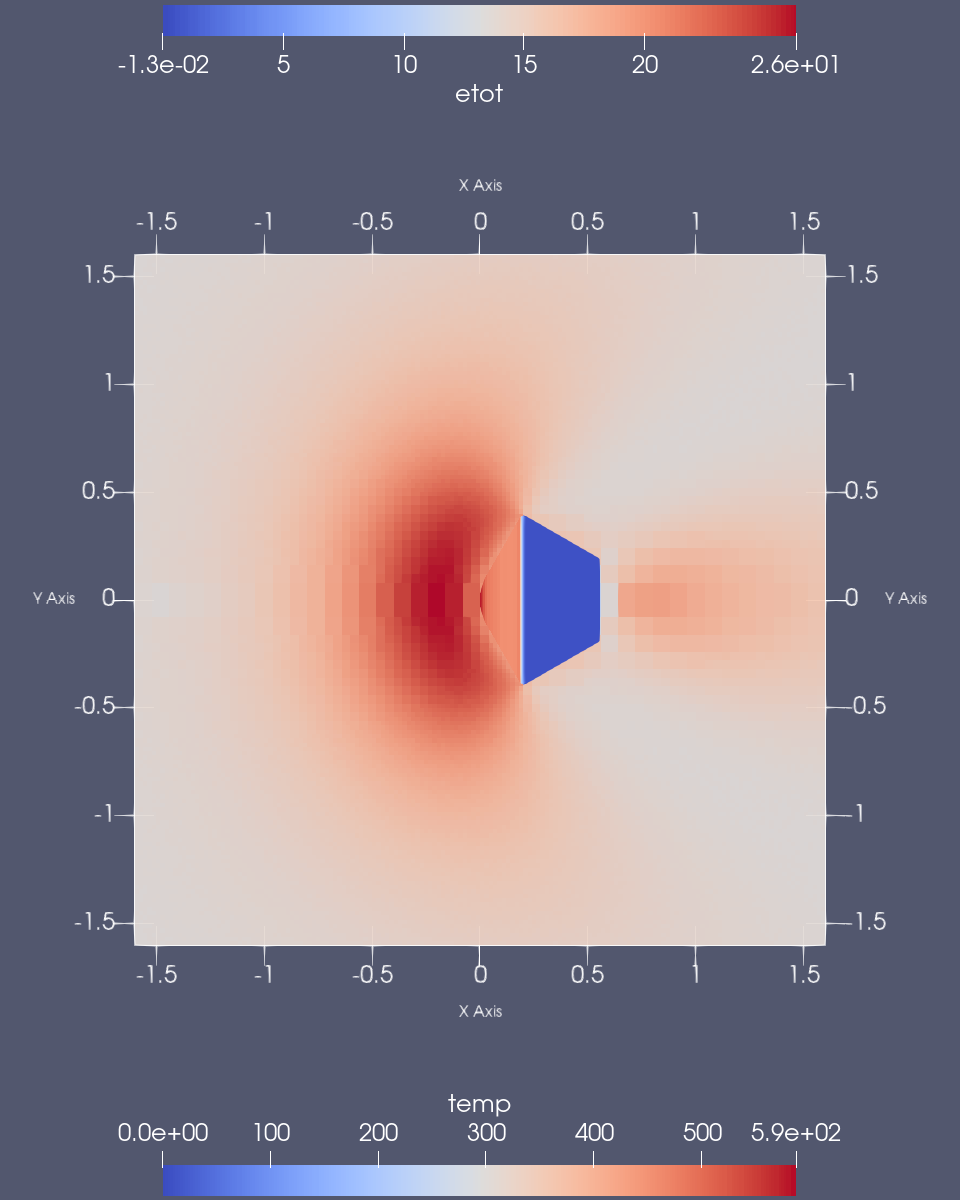
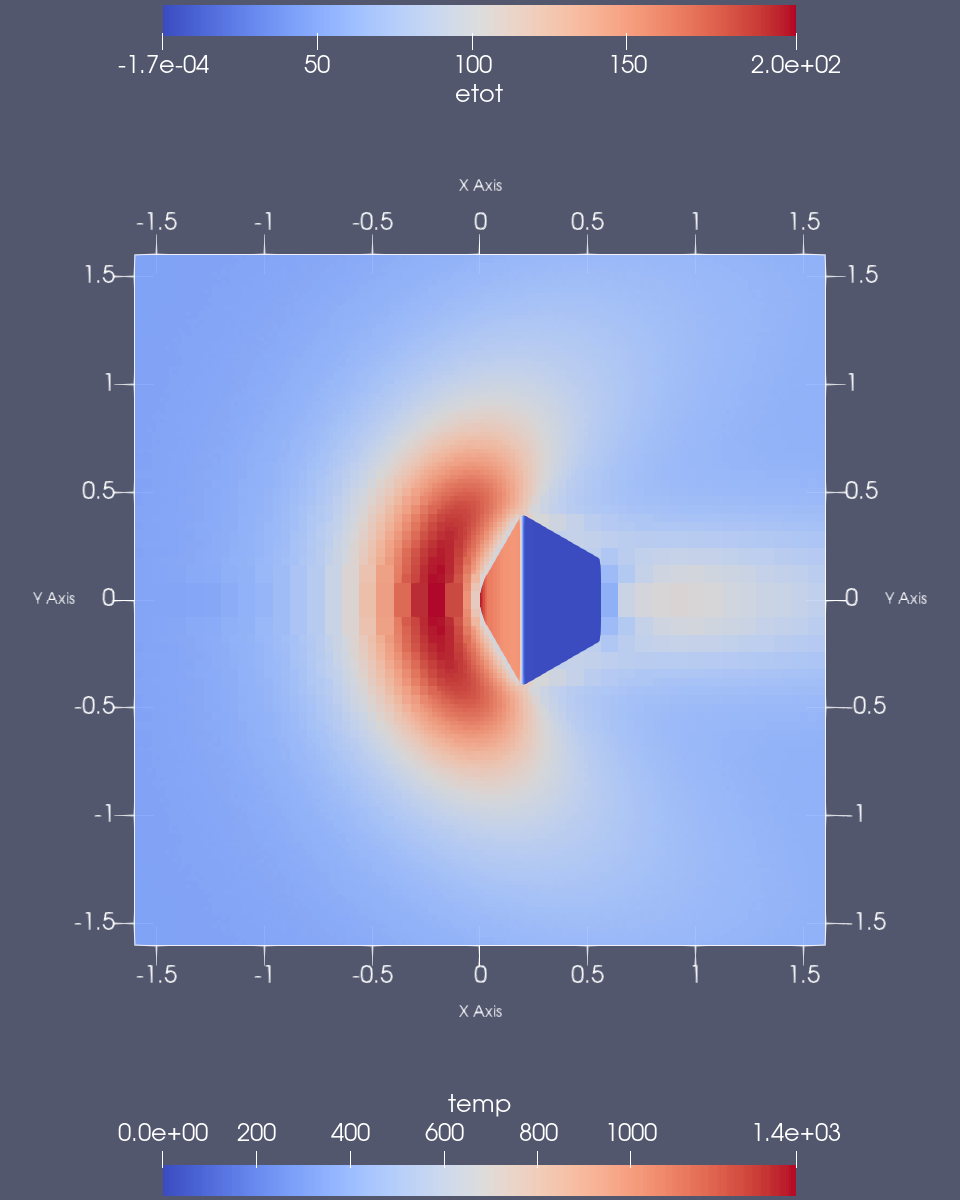
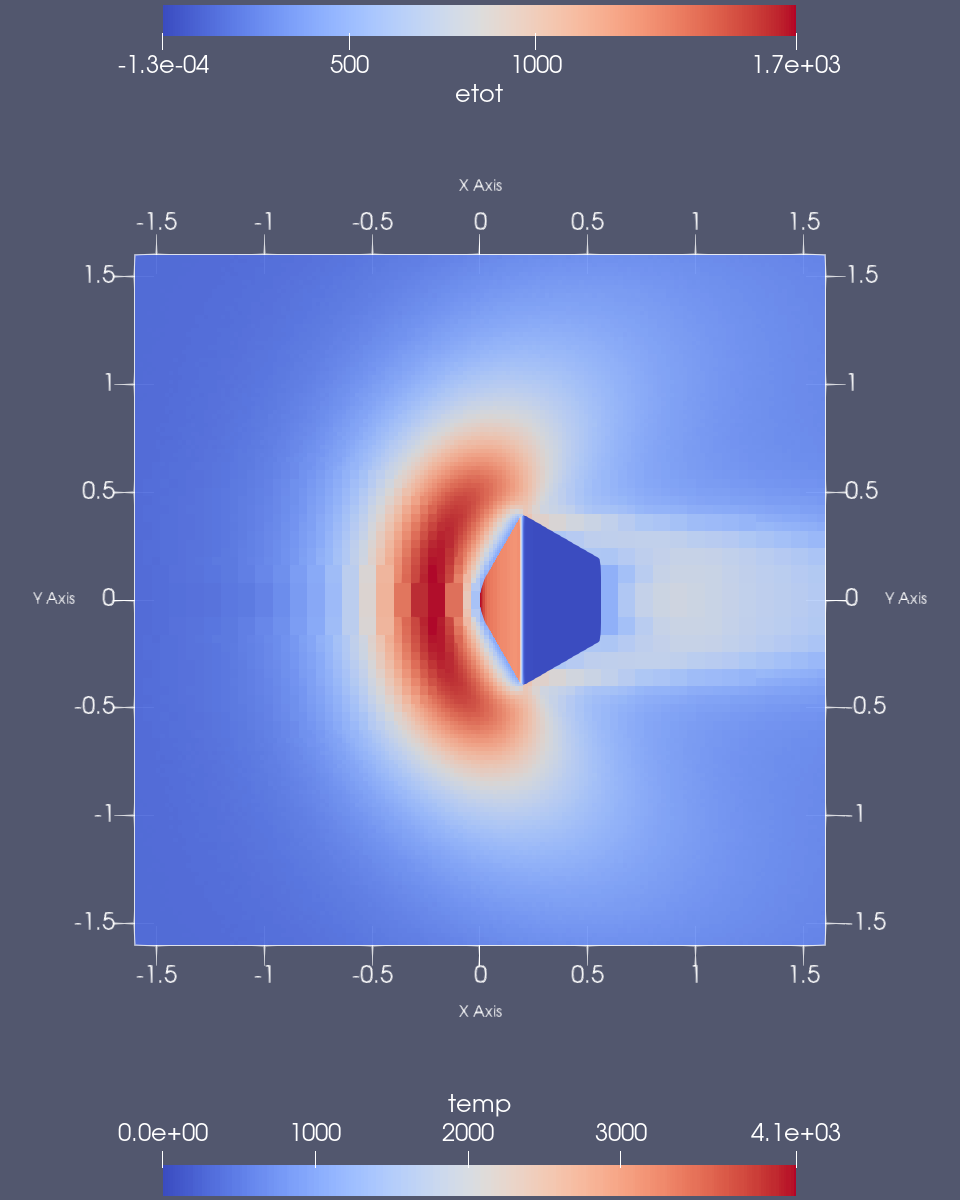
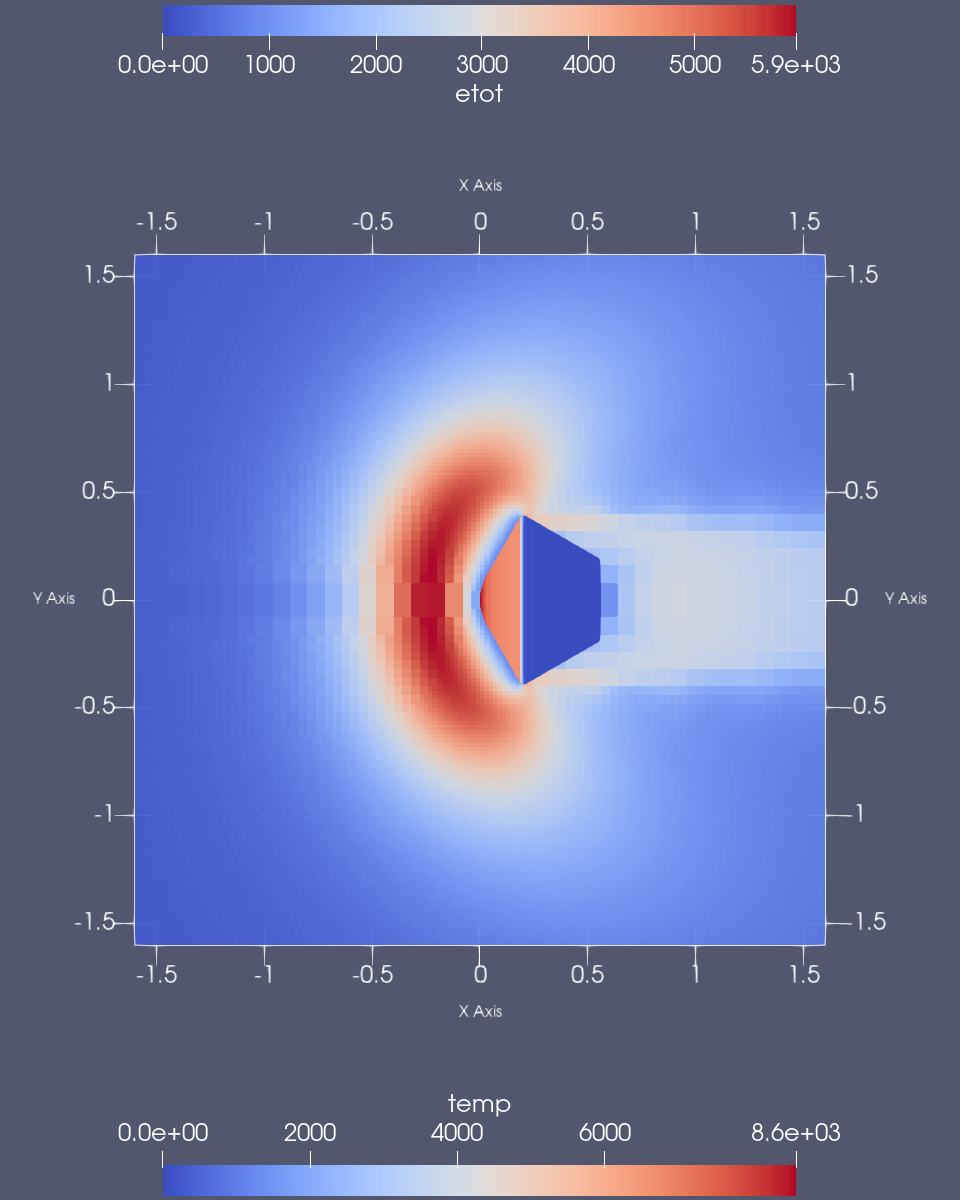
Mach2 | Mach4 | Mach8 | Mach12 | |
---|---|---|---|---|
Temp (K) | 590 | 1400 | 4100 | 8600 |
eflux | 26 | 200 | 1700 | 5900 |
The energy flux is concentrated on the tip. With the Mach number increase, the shape of the tail changed from cone to cylinder.
(ii) Density and surface pressure
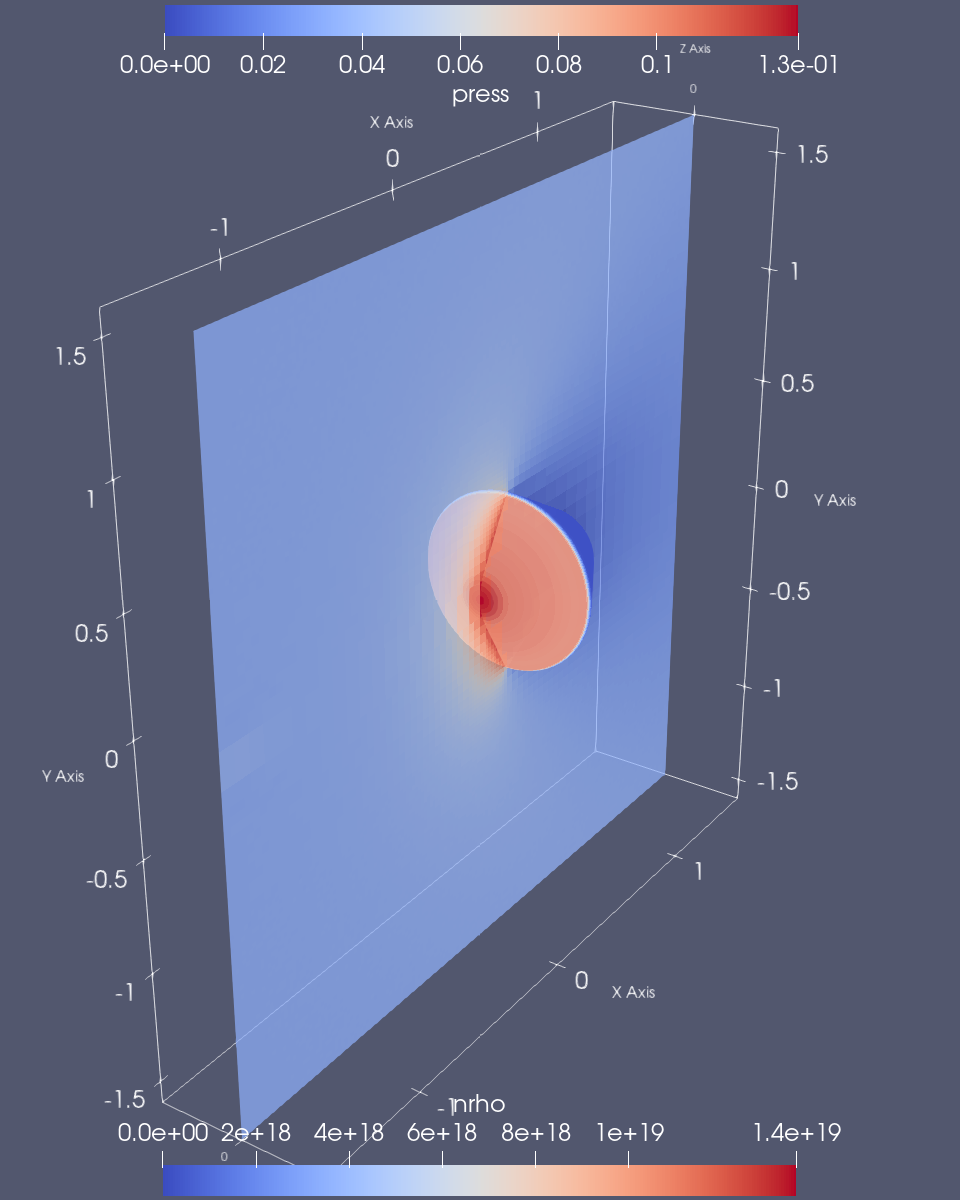
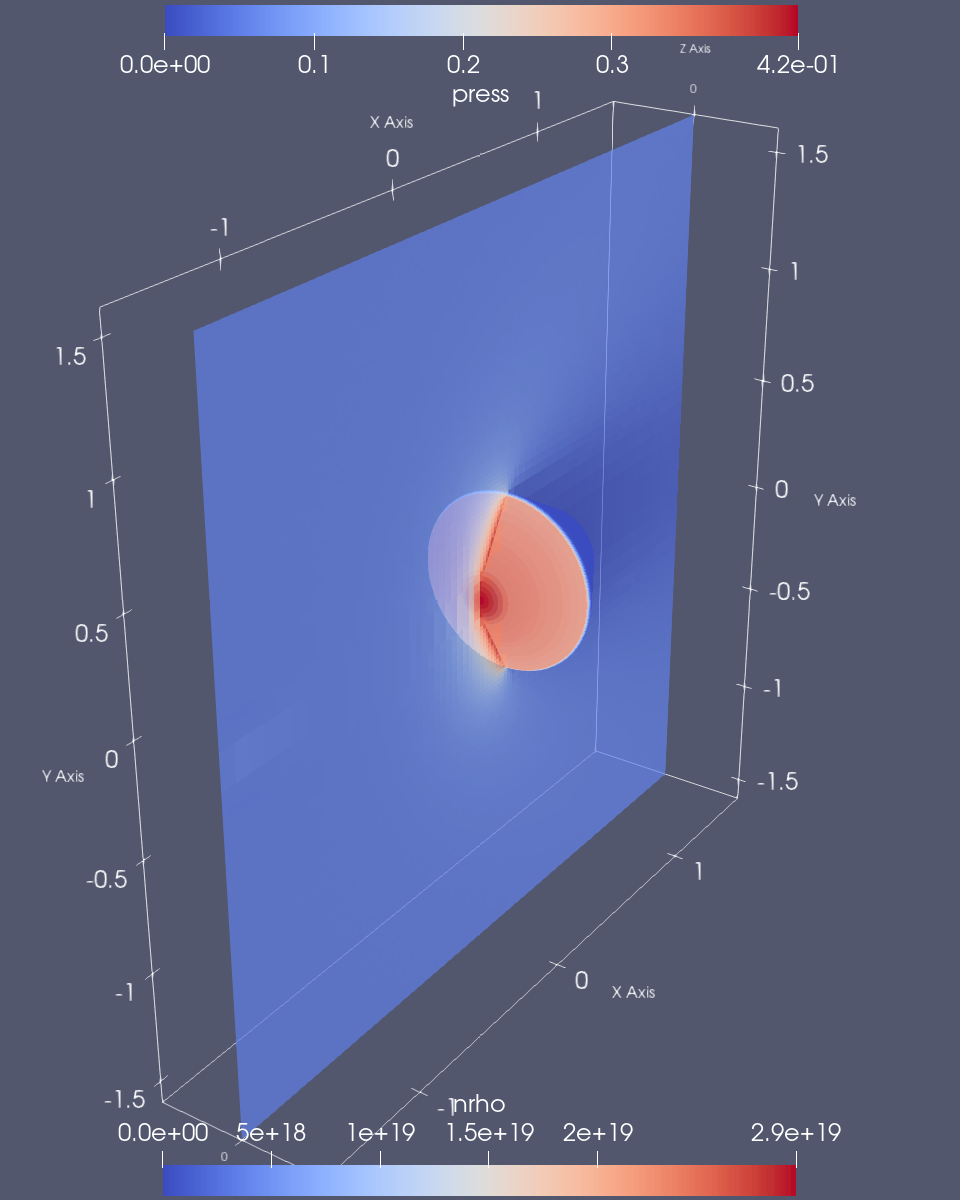
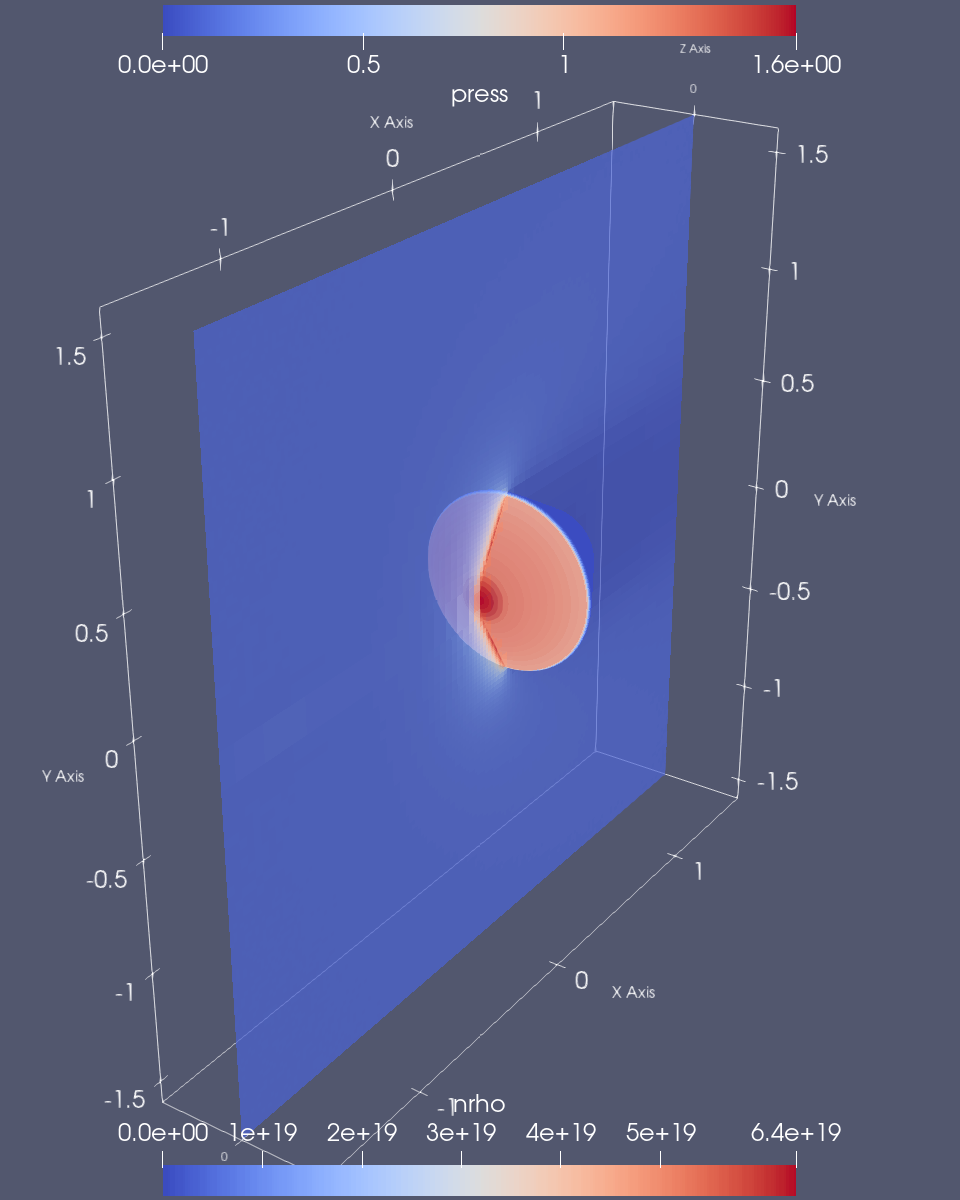
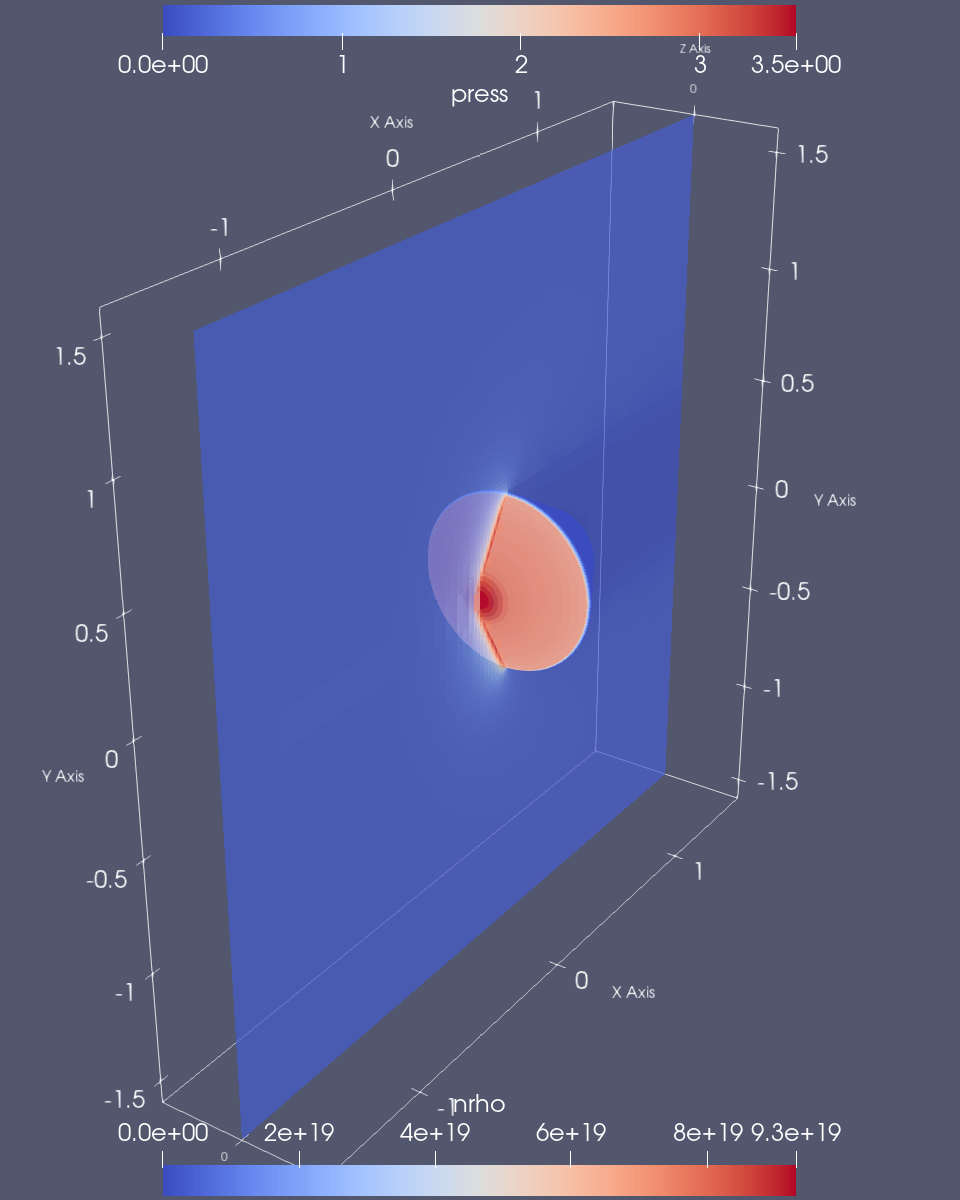
Mach2 | Mach4 | Mach8 | Mach12 | |
---|---|---|---|---|
Dens | 1.4E19 | 2.9E19 | 6.4E19 | 9.3E19 |
Press | 0.13 | 0.42 | 1.6 | 3.5 |
As the speed is faster, the high-density layer gets thinner and the density jump around the tail flow is more significant.
(iii) Velocity and surface shear force
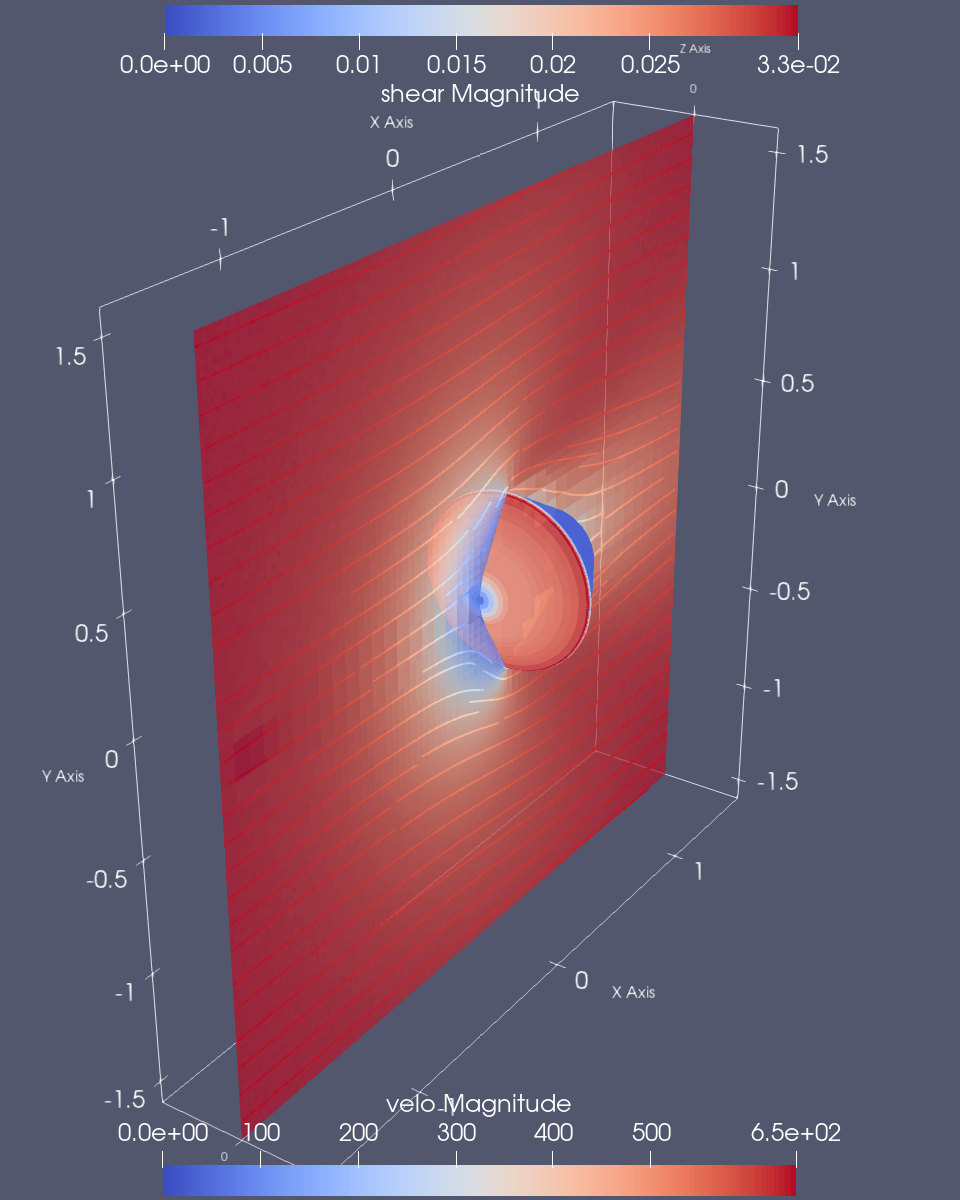
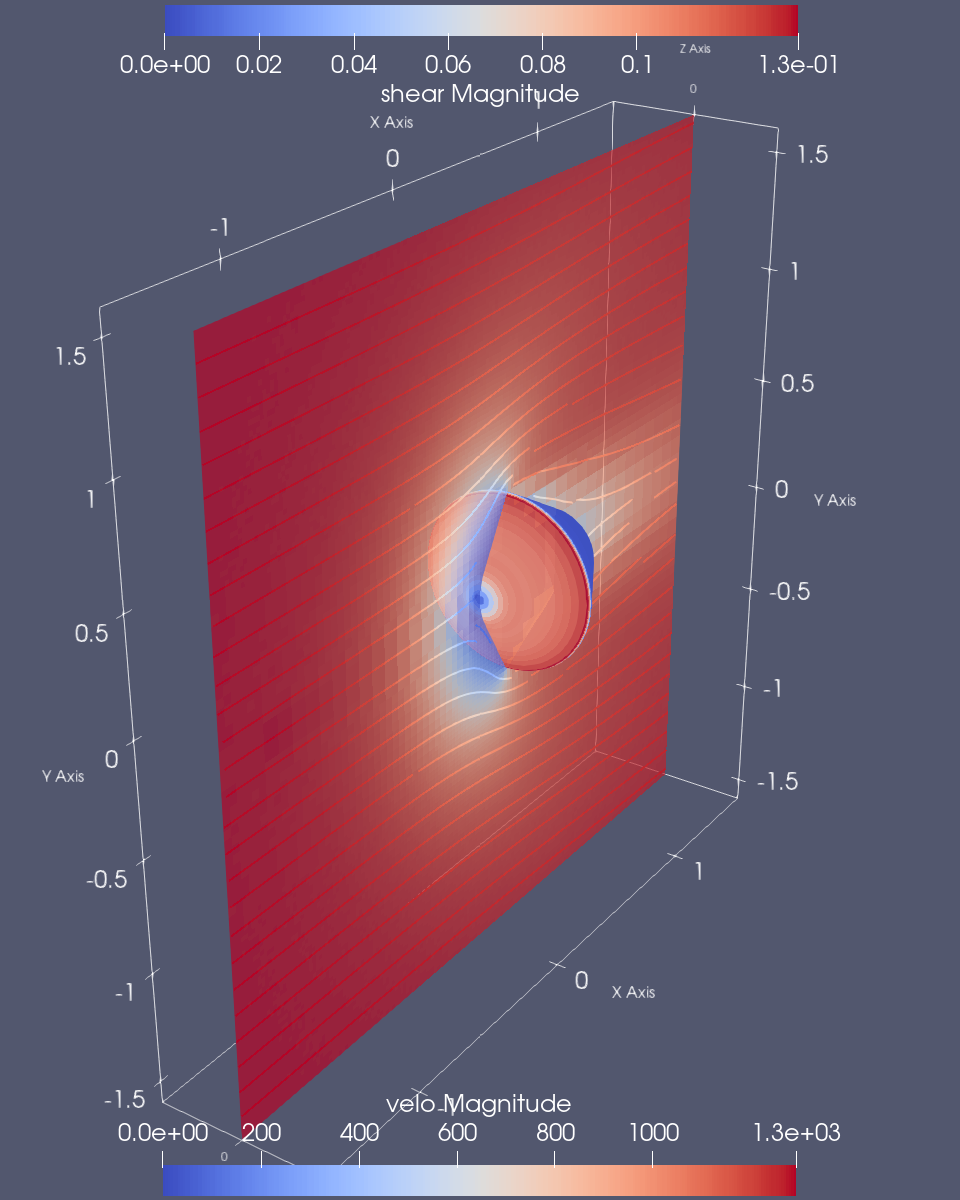
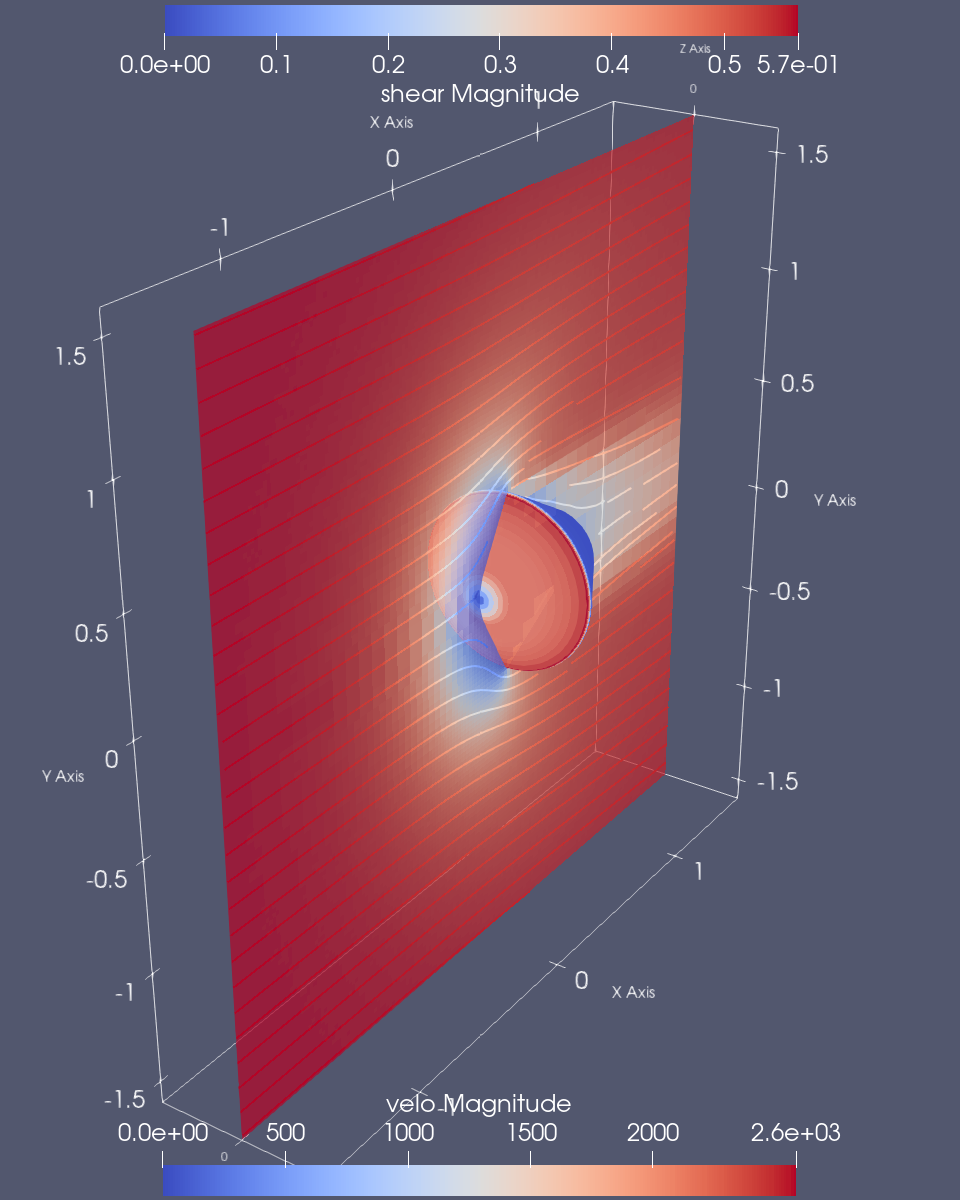
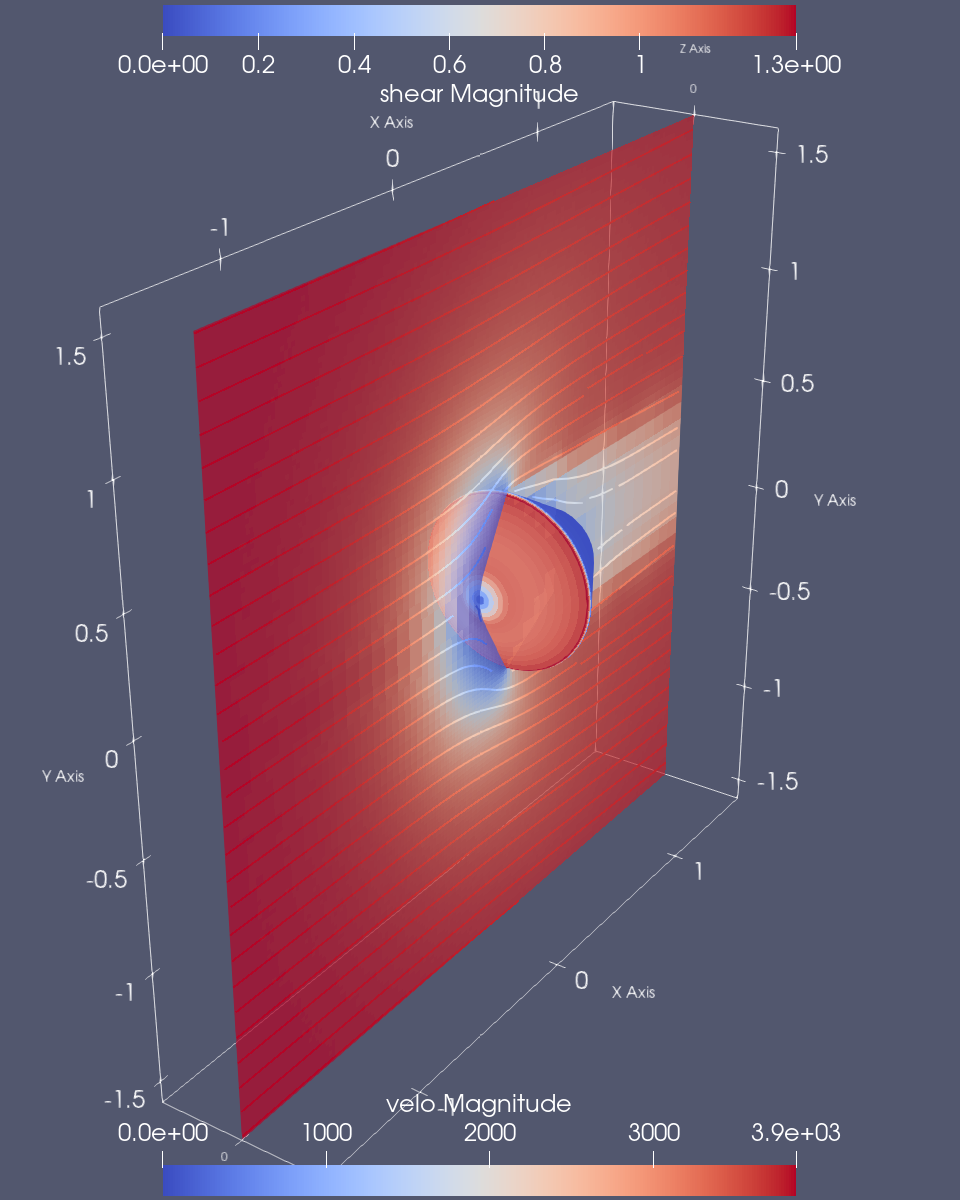
Mach2 | Mach4 | Mach8 | Mach12 | |
---|---|---|---|---|
Velo (m/s) | 650 | 1300 | 2600 | 3900 |
shear | 0.033 | 0.13 | 0.57 | 1.3 |
Shear stress on the surface gets highest at the edge. With the Mach number increase, the flow behind tends to separate faster.